VoluMill – Technological Streamlining With Increased Speed
At the seminar, which was facilitated by the Association of Engineers on "Technological Innovation in Precision Machining" Cimatron revealed the CimatronE-11 version released soon. Among other innovations and developments, the Company's engineers, Shay Aziz and Alon Leuchter, presented the new upgrade in the field of erosion, the VoluMill module.
For several years now, there are a number of established and proven processing technologies in the market, promising the removal of a material in large volumes and in a short time, while maintaining the tool’s lifespan. These technologies, efficient especially for hard materials (various steels, titanium etc.), are usually based on rapid circular motion, while maintaining uniform tool load, characterized by a small lateral stride and a large chip depth. The upgraded toolpaths can be seen in Figure 1.
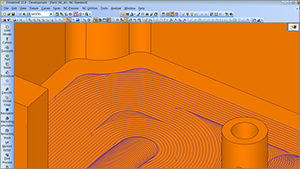
One of the pioneers in that field of processing technology is American VoluMill software. The advanced capabilities of Volumill have been successfully integrated, more than three years now, in GibbsCAM software of Cimatron. The uniqueness of the VoluMill module is the ability to perform rapid removal of maximum raw material amount resulted in preliminary processing. Using this technology is primarily reflected in processing hard materials that are too stiff for processing, as well as having wearing effects on the tools.
In light of our successful experience with Volumill technology, we decided to incorporate it in CimatronE-11, to allow our customers benefit from this advanced milling capability, for 2.5-axis processing, as well as three-dimensional models processing.
The guiding principle when calculating toolpaths in accordance with the processed surface topography is "maintaining a uniform tool load". One of the problems in wearing of breaking of tools is the changing load on the tool during direction changes; therefore, the mathematical algorithm on which the software is based uses the calculation of the chip intended to be removed throughout the tool; at the same time, toolpaths are adjusted depending on the volume of raw material at any given moment, and in accordance with the guiding principle of maintaining a uniform tool load.
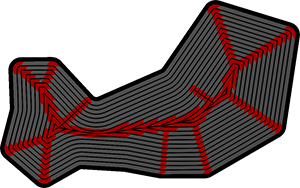
For example: "pocket" processing shown in Figure 2. In the traditional processing which is incorporated in the existing CADM software, we see areas where the load on the tool is heavier (highlighted in red) than that on the rest of the processed area. In these areas, the tool is largely and intensely in contact with the material, which causes entrenchment. As mentioned earlier, this is one of the most serious problems during milling process. In order to maintain the tool during traditional processing, the user must change the conditions of processing, reduce progression, reduce chip depth, or reduce lateral stride. Unfortunately, these changes cause extended manufacturing time and higher costs.
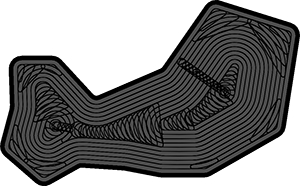
Thus, the ideal solution displayed in Figure 3, which is calculated by Volumill, is a change in the toolpaths, while maintaining uniform volume; during progression changes, the uniform load on the tool is also maintained. The toolpath is characterized by tool’s rounded and consistent toolpaths.
Despite the length of toolpaths, which is significantly longer than the traditional one, due to reducing the lateral stride (approximately 7% of the vessel diameter is recommended), but we use significantly higher progression and greater chip depth to, up to 2.5 times of the tool’s diameter.
These conditions lead to reduced processing times while maintaining longer tool’s lifespan.
In order to determine optimal conditions of processing, we can use the data calculator attached to the Milling Advisor software; the user enters all the data necessary for determining the processing parameters, such as: type of raw material, hardness of raw materials, tool diameter, number of teeth, tool coating, mounting level of raw material in the facility, type of gripper in the machine, gripper tightening method, maximum axis speed and the maximum machine progression speed.
After processing all the data entered to Milling Advisor, the calculator will recommend on relevant processing data for the current processing, which can be differed by the level of aggressiveness selected by the user.
As part of defining the conditions of procession, including the level of aggressiveness, VoluMill offers several levels of aggressiveness in a processing mode (Slotting – initial processing) while changing the lateral stride and calculating the progression that changes on any point on the toolpaths, as we see in Figures 4-6.
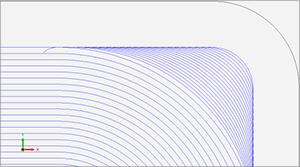
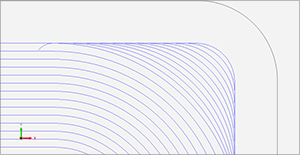
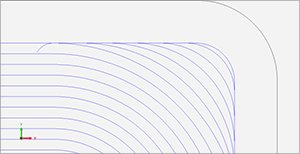
VoluMill software is a standalone product, but as detailed above, VoluMill software is an integral part of Cimatron.
Thus, the user can enjoy the two worlds: a rapid removal of a considerable amount of material, while preserving long tool’s lifespan using VoluMill module; and CimatronE intermediate processing and final processing to achieve high surface quality in a minimal processing time.
In conclusion:
The use of VoluMill technology benefits the user with shortened processing times - up to 3 times shorter than current traditional practice. This streamlining is a result of significant reduction in milling time, extending tool’s lifespan and maximizing machine capabilities.