CADM Development Process in Parallel to the Milling Machining Progress
Throughout the course of its existence, the concept of "CADM" (Computer Aided Design and Manufacturing) has addressed the difficulty and complexity of developing a processing program which encompasses the entire manufacturing process, from beginning to end, taking into account the limitations of manufacturing, using existing technology and meeting delivery times.
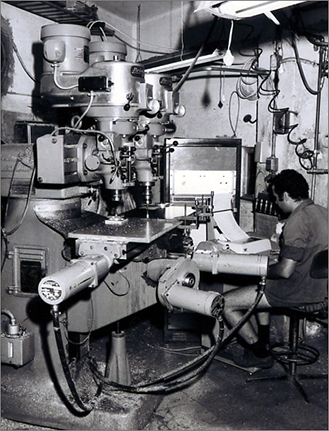
The birth of CADM has occurred somewhere in the seventies of the last century; it began to weave shape in the eighties and was given a boost and a quantum leap with the invention of the personal computer (PC) and the operating system DOS; its present form began to take shape in the nineties with the release of Windows operating system. This article will describe the different stages in the development of CADM in parallel to the development of the common CNC (Computer Numerical Control) machines, with a view to the future.
There is no dispute on the fact that even before the seventies of the last century, machines were manufactured with thousands of components, using precision machining, such as jet aircraft, spacecraft, vehicles and more; but the technology used to manufacture the components became obsolete and slowly disappeared, while more modern, quick, minimized , well-designed and accurate technology has taken its place. In order to reach this manufacturing technology, as well as meet stringent requirements, the CADM is required.
Metal processing began in the Iron Age, 1200 BC and lasted until the present day - only the methods have changed. The use of modern precision machining began early last century, but was manual, complex and required excellent technical ability. Eventually, in the sixties and the seventies of the last century, the computer was called for the mission and became an integral component of the machine.
During that period, the computer, or better known as the "Numerical Control", began to control the toolpath. The size of the computer was the size of a small room or a large closet, and work was carried out slowly and patiently. The working method was "open loop" which means delivering the positioning data to the axis engines, continuously, by the computer, but without the ability to receive a response on completing the task, and whether the axis reached the desire and exact location.
With the development of computer capabilities, and shrinking its size, the ability to work in a "closed loop", in which the computer monitors the axis position at any given time, and repairs itself as needed, evolved.
Precision machining with such abilities, which are also called CNC machines, are common in all branches of the metal, wood and plastic processing; they require the operator to have some computer knowledge that was not required in the past. Using CNC for precision machining requires developing a Gcode that contains positioning toolpaths and activation and/or deactivation commands for the various components of the machine.
The invention of the CADM in the late seventies was designed to address the development of a Gcode code, which is adapted to the language of the various machine controllers. Cimatron, in its early days in the eighties, began to provide full and comprehensive resolution for the process of planning and mechanical production, with the development of an integrated technology (IT) product. Initially, the IT product could only basic actions, and was like working with a two-dimensional drawing board; it had a limited ability in producing a basic Gcode code for precision machining, which encompassed most of the processing technologies at that time.
Running the code was complex and required a highly skilled operator that had full control over computer operation, as well as extensive knowledge of precision machining.
The final stage of producing the Gcode program was transmitting the program to the machine. Those years the machines could only read "punched card" only, so it was necessary to create a punched card containing all the program data by punching holes (8 holes across) indicating the letters and numbers. The punching machine was called "Teletype", and was connected to the computer. After the punching, it was transferred to the machine’s reader and the data was entered to the machine.
Initially, the CNC machines were working as a combination of two axes - X and Y, for producing components with smooth working surfaces, when the Z-axis was operated manually or computer-controlled but not simultaneously with the X-Y axes. Later, when computer capabilities have progressed, all the three axes, X-Y-Z, were incorporated to work simultaneously; it led to the development of the ability to create three-dimensional components with inclined or amorphous surfaces.
In order to provide three-dimensional design solutions, Cimatron put efforts to develop and launch versions of spatial precision machining capabilities. In those years, CADM software was working on "strong", large and bulky workstations. The cost of hardware to run the basic CADM software was 40,000$ for each workstation, which is today considered obsolete. With the development of the DOS-based PC and the 5.25" floppy disks, the CADM software were developing a friendly and accessible products that could be used in every precision machining plant. Certainly, in parallel with the improvement of the processor and screen color spectrum, the CADM capabilities strengthened and we got to see Cimatron’s flagship product of working on a two-screen computer, to display operational commands and graphics. The software allowed the user to design and manufacture components using three-dimensional milling while displaying simulation and producing a perfect Gcode program.
At the same time, precision machining manufacturers were working in collaboration with manufacturers of CNC controllers, to launch CNC machines with faster and generally improved controllers, and most importantly, included standard memory, which allowed storing the CADM-generated Gcode programs, which become larger, depending on the complexity of the component to be produced. Additional capabilities which have been enhanced in the machine controller are the direct link between the CADM computer and the machine via RS232 communication port, which completely eliminated the need for cumbersome pierced films. This data transfer capability enabled the operator to store the Gcode program in the memory, or work online, where the communication computer is enslaved to the machine and "pushes" the Gcode program throughout the processing; as a result better surface quality can be achieved, since the size of the program produced by the CADM-generated Gcode processing provides better resolution, very high accuracy and min
imum tolerance from the complex surface to be processed.
Today, almost all the modern CNC controllers are characterized by the ability to store indefinite amounts of data; they contain a hard disk or a giant memory that allows continuous and efficient work on a long processing program, and consequently – a superior surface quality, in a shorter operating time. The data transfer is done instantly by standard network.
Throughout the years, computerized milling machinery became more and more complex; 3-axis machines were added an additional axis on the table and they became 4-axis machines (XYZA), or an addition of one axis combining two axes, which created 5-axis machines (XYZAB). Most of those machines can combine simultaneously all five, which allows the manufacturing of even more complex components; today, almost every component can be processes in a single mounting, allowing completing the work on five sides simultaneously.
In order to upgrade the machining process, machine manufacturers have decided to combine the fourth and fifth axis as integral component of the machine’s structure, and categorize the machine as a dedicated 5-axis machine with high accuracies in all five axes and simultaneous toolpath, while achieving smooth surface quality, with no signs of deceleration.
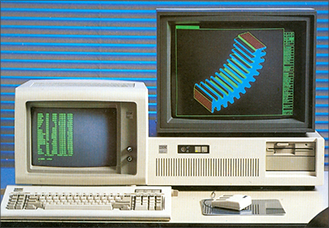
These machines have become more and more common among precision machining plants in Israel and abroad. As a result, the need to develop CADM software dedicated to a five-axis programming, which meets all requirements of manufacturing and supporting the existing new precision machining technologies. The first and most important demand of all – for a simultaneous 5-axis processing program – user-friendliness, including a fast and intuitive learning curve, which provides the user with control and intervention abilities, during the different stages of technological processing. Cimatron has worked diligently to launch a product that meets the user's requirements while providing a complete solution for those complex machines, as well as generating a Gcode program which does not require any manual editing.
The software provides a solution for 5-axis-character components of all types, i.e. components requiring indexical processing (working on all five sides of the cube, so that the 4-5 axis is placed in a certain angle and the work is done on three axes only – on one side of the component).
Component processing with Cimatron Indexical 5-Axis Technology
Furthermore, the software provides a comprehensive solution for processing components with a simultaneous 5-axis character (continuous processing of all sides, when all five axes move simultaneously and process the component from all sides accessible, and with regard to the technological limitations of the machine).
Component processing with Cimatron Indexical 5-Axis Technology
Another feature when using Cimatron software for 5-axis programming is full simulation of the entire processing, including machine simulation taking into account the different precision machining tools, as well as the mounting devices, which mount the component on the table. This feature enables the user a self-check, as well as the results of the technological process. This simulation will display conflicts, if any, between various machine components, tools and the component being processed.
A recent development of mechanical technologies enables machine manufacturers to upgrade the performance level for the customer. Today, CNC machines with an idle speed of up to 90 meters per minute. The speed stems from the development of linear motor which eliminate the need for the conducting screw, so that the engine itself performs the table movement against the machine’s body.
Further development which is aimed to conquer the precision machining market involves moving the machine’s components according to electrical changes of the magnetic polarity of those components; this way, the table can move on the machine’s base without any friction, since during the toolpaths it rises minimally (a micrometer = a thousandths of a millimeter) above the machine’s base, due to the magnetic rejection between them. As a result of the friction, incredible speeds can be reached; since all the motion and control components are electric, rather than mechanic – the accuracy during work can reach its maximum. Table movements in respect to the axis are contiguous rather than fragmented, since there are no mechanical elements, such as screws, bearings and motors, which lead to losing the sequence of toolpath at each change of direction.
Certainly, all these innovations improve the duration of manufacturing and increase precision, but in order to get the most from this technology, it is necessary that the CADM software can generate a processing program which supports the abilities of these machines. In the Cimatron software, for all types of processing ranging from 2.5-axis to 5-axis, there is an HSM (High Speed Machining) option as an integral and standard part of the software.
HSM option is characterized by unique processing strategies which maintain a uniform motion sequence that enables the machine to perform the precision machining smoothly. This processing will lead to faster results (improvement of about 30% in manufacturing time), more accurate and with better surface quality (thousandths of a millimeter).
Followed by further development of CNC machines, a Micro-Milling niche was developed. Micro-Milling is processing of miniature components processing tools tenth-of-a-millimeter in diameter (and even smaller than that). The use of small diameter tools requires special changes and, while addressing toolpaths differently, in order to maintain the integrity and ability to work continuously. Necessary conditions for precision machining: 1. rotational speed must range from 18,000 rpm to 80,000 rpm; toolpaths must be continuous, enabling the machine to progress without changes in acceleration and deceleration; 2. Removal of a uniform volume for duration of processing.
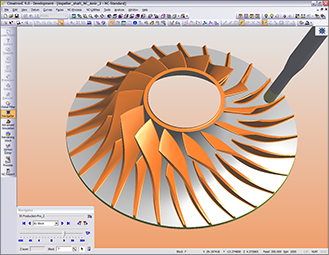
The machines must have a resolution of one thousandth of a millimeter motion at least, high accuracy and repeatability of an order of a thousandth of a millimeter; it must be stable and free of vibration; and above all, integrated with a fast computer that can read a program consisting of thousands of short toolpaths and run it continuously, under the required terms of precision machining.
Also for this niche of micro-processing, Cimatron developed unique module which is an integral component of the extensive program; the program takes into account all the stringent constraints when using Micro-Milling processing. The Cimatron Gcode program will contain all the technological constraints necessary for working with these miniature tools.
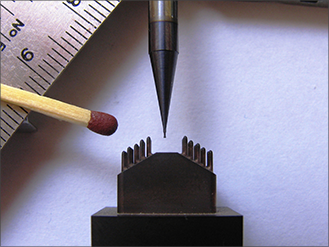
The vision of ultimate solution is not yet achievable, but according to the growing technological abilities presented in this article, we can say with confidence that the sky is the limit and that we are not far from the day when we can plan, design and produce all that we desire. Cimatron is preparing for the future by improving the interaction between the user and the software, as well as implementing "human intelligence" as an integral component, in order to reach a technological process which is no less than the ultimate vision of precision machining."